The Process |
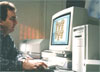 |
Designing
A state-of-the-art designing facility through both, Computers and Manually facilitates us preparing the best modeling for part and tooling development. |
|
Dies
& Tooling
An In-house Die-shop equips us for fabricating all types of dies and tooling, using machines such as : Plano Milling Machines, Spark Erosion Machines, Copy Milling Machines, Heavy Duty Lathe Machines, Die Sinking Machines, Vertical Band Saw Machines, Heavy Duty Pillar Drilling Machines etc.
Dies are produced using Wooden Pattern Graphite Electrode. Full sets of templates are fitted on sinking of the die for rigid dimensional checks and inspection. |
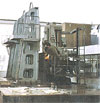 |
|
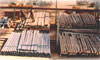 |
Raw
Materials
Materials is procured from reputable approved Steel Mills in form of Cast Billets, Blooms, Rolled Billets etc. , in various Size as per the requirement of the final product.
Our well-set inward process automatically checks for the quality of the Material. Materials of different types are stored separately with color codes marked, to Facilitate full traceability and avoid material mix-ups. |
|
Cutting
Most cutting of raw material is done with the help of 2 No’s of 800 T Capacity Shearing Machines and Band-Saw Machines.
Color codes are marked on Cut pieces and are stacked separately with a Banner fixed over each stack so as to identify the materials grade and also the final product to which they are meant. Stacking is always done in such a way so as to ease lifting and moving through Fork Lifts. |
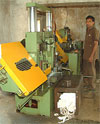 |
|
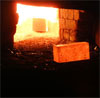 |
Heating
Cut pieces are heated in Pusher type forging Furnaces fitted with Temperature Controller. The pieces are carried to the forging hammers through over-head traveling Mono Rails. |
|
Forging
The process of forging is carried out on Pneumatic Forging Hammers of 3 to 10 T Capacity. The metal is shaped to a part by Hammering the hot cut piece between the Top and the Bottom dies fixed on the Hammer. The finished product through this process is much more reliable for strength and quality than a similar product produced by casting, pressing or machining. |
 |
|
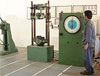 |
Post
Forging Operations
Depending upon the specifications required for the end use of forged component and as specified by the customer, forgings undergo further process such as Heat Treatment and Shot Blasting, Hardness testing and crack detection. We have an In-house facility for these processes. |
|
Machining
We are situated at the place where we have a number of ancillaries engaged in doing the machining jobs. Whenever required we can out source CNC Machining, Drilling, Threading, Capping and Grinding etc., from your quality-approved ancillaries. |
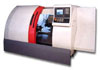 |
|
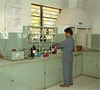 |
Quality
Assurance
The quality checks set up within the procedures is performed to maintain complete control of each order. The quality check begins with receipt of raw material and continue during set up, forging run, which includes Hot Inspection, Secondary Operations and Final Inspection. Samples are checked for dimensional accuracy and metallurgical soundness. Samples of hot forgings are inspected at intervals for forging defects and dimensional accuracy. The inspection process also includes hardness testing and crack detection. |
|