The Process |
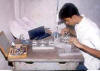 |
Tooling
A tool maker build a precision die to make wax replicas of the part called patterns. Before start the casting process, injunction die is constructed to produce wax patterns. This tool is constructed from Aluminum or hot die steel material, for most applications, single/multi cavity dies are used for high production quantities. |
|
Pattern
Injection
Molten wax is injected in to the die cavity. The resulting pattern is removed after it solidifies. This pattern is an exact replica of the metal part to be produced, with the allowances added to compensate for volumetric Shrinkage during the process. This ax pattern are inspected, cleaned before set-up on wax-Spares. |
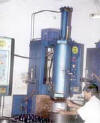 |
|
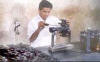 |
Pattern
Assembly
The individual wax patterns are assembled on to a wax Spare to form a mold or tree/cluster. The number of patterns are assembled per tree varies, dependent upon the size, weight and configuration of a given part. |
|
Shell
Building
The Cluster or tree is dipped repeatedly in liquid binder and Ceramic powder to build up a shell mold. This process is repeated several times until a specified shell thickness results. The ceramic shell range in thickness from 5mm to 12mm depending on the size of the part being produced. Now, the molds are moved to a controlled drying area for completely dry before de-waxing. |
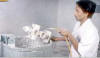 |
|
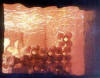 |
De-Waxing
& Pre-Firing
The wax is melted out, leaving a hollow ceramic shell. The moulds are pre-fire to fuse the ceramic particles together, so that the mold can withstand the pressure & temperature of the molten metal being cast. |
|
Casting
The Molten metal is poured in to the preheated molds and solidifies to form a cluster of castings. |
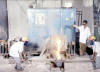 |
|
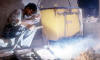 |
Cleaning
& Casting Removal
The Ceramic Shell is removed form the metal mold with the help of pneumatic hammer or high pressure sand blast machine.
The individual parts are then cut-off from the runner with the help of welding machine or cut-off machine.
The gates are ground to the desired dimension utilizing fixturing.
The parts are than deburred & sent for secondary operations such as heat treating and then finally will goes in sand/shots Blasting.
After the final surface preparation each part is inspected to guarantee is meets as per the specification and customer requirement. |
|